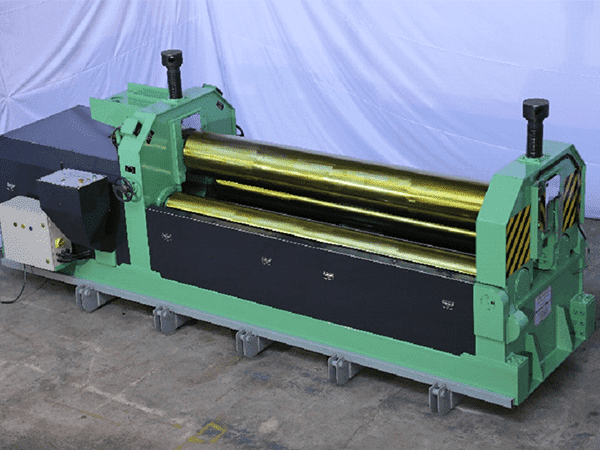
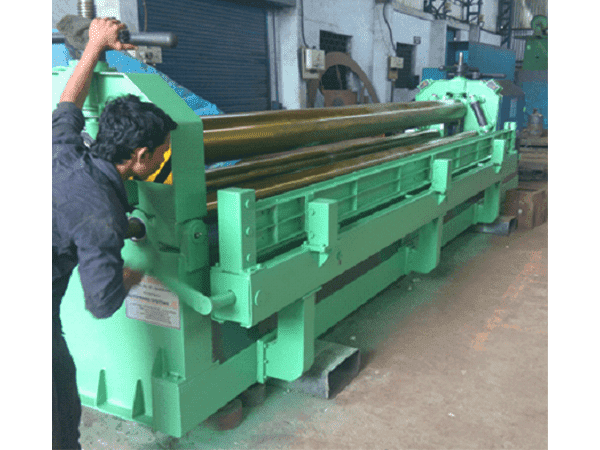
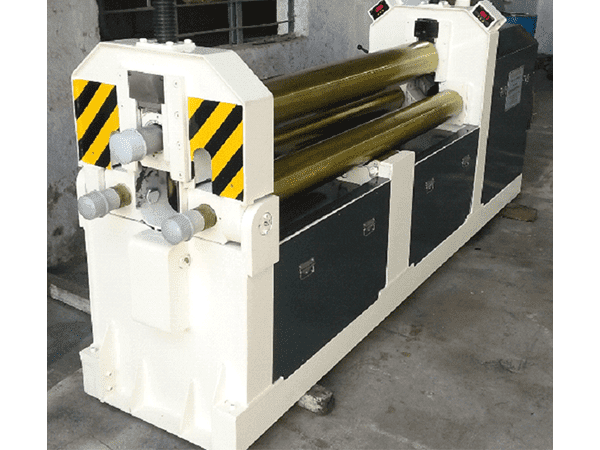
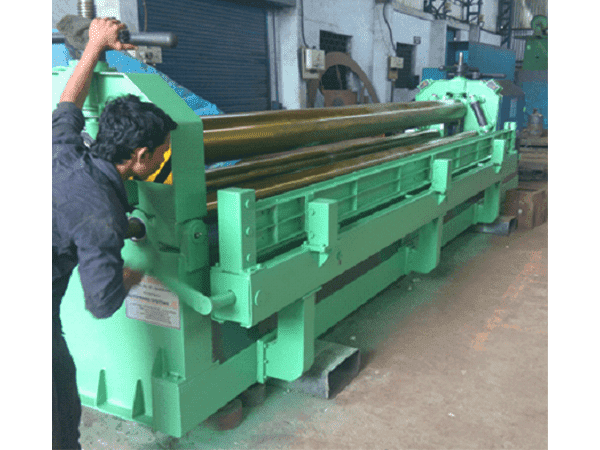
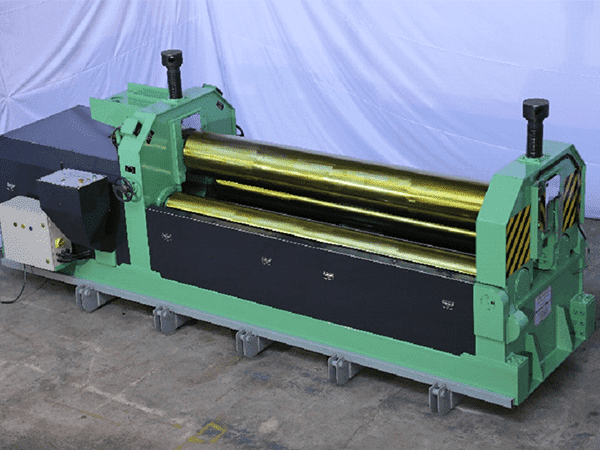
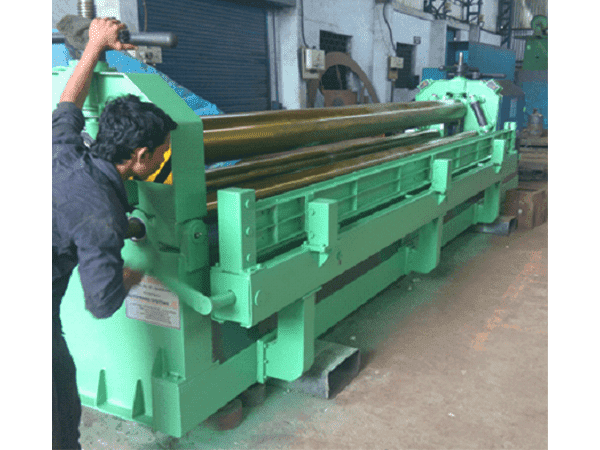
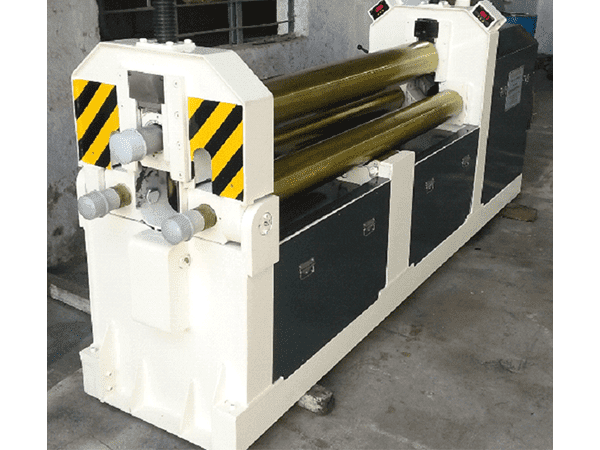
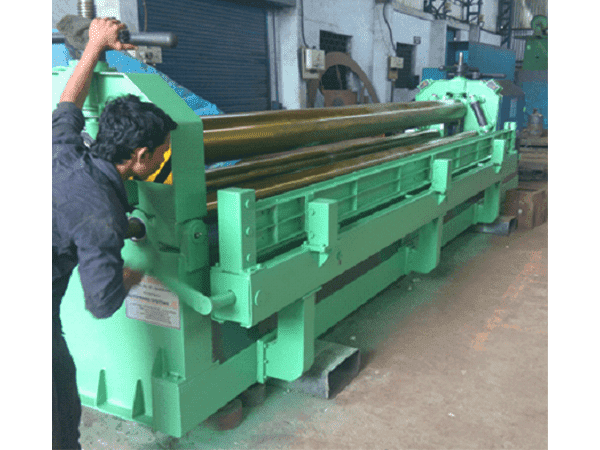
WORK PIECE READY DULY PRE BENT/PRE PINCH
ROLLING STARTS
ROLLING START IN SINGLE PASS
ROLLING IN PROGRESS (MULTIPLE PASS)
ROLLING IN PROGRESS
ROLLING COMPLETE
Sr. No | Particular | Remark |
---|---|---|
MODEL CODE | 3 R FAMN | |
1 | PRE BENDING | NO |
2 | ROLLING/BENDING | YES |
3 | MAX ROLL WIDTH | 4500 MM |
4 | MINIMUM THICKNESS | 1 MM |
5 | MAX. THICKNESS | 32 MM |
6 | PRODUCTION RATE | NA |
7 | TOP ROLL UP DOWN FOR RADIUS FORMING | MANUAL SCREW ROTATION |
8 | SIDE ROLL ROTATION | ON FIXED AXIS |
9 | ROLL ROTATION | MOTORIZED |
10 | ROLL POSITION INDICATOR | DIGITAL INDICATOR |
The machine is most economical model among all plate bending machine and is most useful for small fabrication shop. Both pre bending and rolling can be done in the same machine.
The machine frame is fabricated from all tested steel plate material. A Die Penetration test is carried out on all weld joints to ensure sound weld quality This frame is subjected to stress relieving, sand blasting and epoxy primer painted for corrosion free long lasting machine life.( Primer paint 160 DFT) The complete body frame is machined in CNC machine to achieve built in accuracy
A tilt able control desk is conveniently located on machine. The main panel start / stop buttons and roll rotation fucntion (Reverse / forward) is provided on the same. The Top roll left side position and right side position are indicated separately by two digital meters
A specially designed & built mechanism allows drop end frame to tilt down in horizontal position without much efforts (one person can perform job). No need to dismantle frame from main body like in conventional machine. The top roll can be tilted to great degree of inclination making it most convenient and ease to remove rolled shells without any difficulty
All our machine rolls are mounted in heavy duty roller bearings. Each roller is fitted with two bearing per side (four bearing per roller).
A dual cone bending device can be provided as shown. The attachment provided between bottom rolls is suitable for narrow cone diameter. The attachment to be fitted on a main frame is suitable for cone having wide angle.
An extra wide 'Y' type adjustable support rolls mounted in bearings provides best support to bottom rolls & eliminate scratches on top rolls
An extended rolls can be provided for mounting dies to roll different sections like angle, channel, beam, pipe or flat etc.